Manufacturing Excellence: AI Agents for Predictive Maintenance
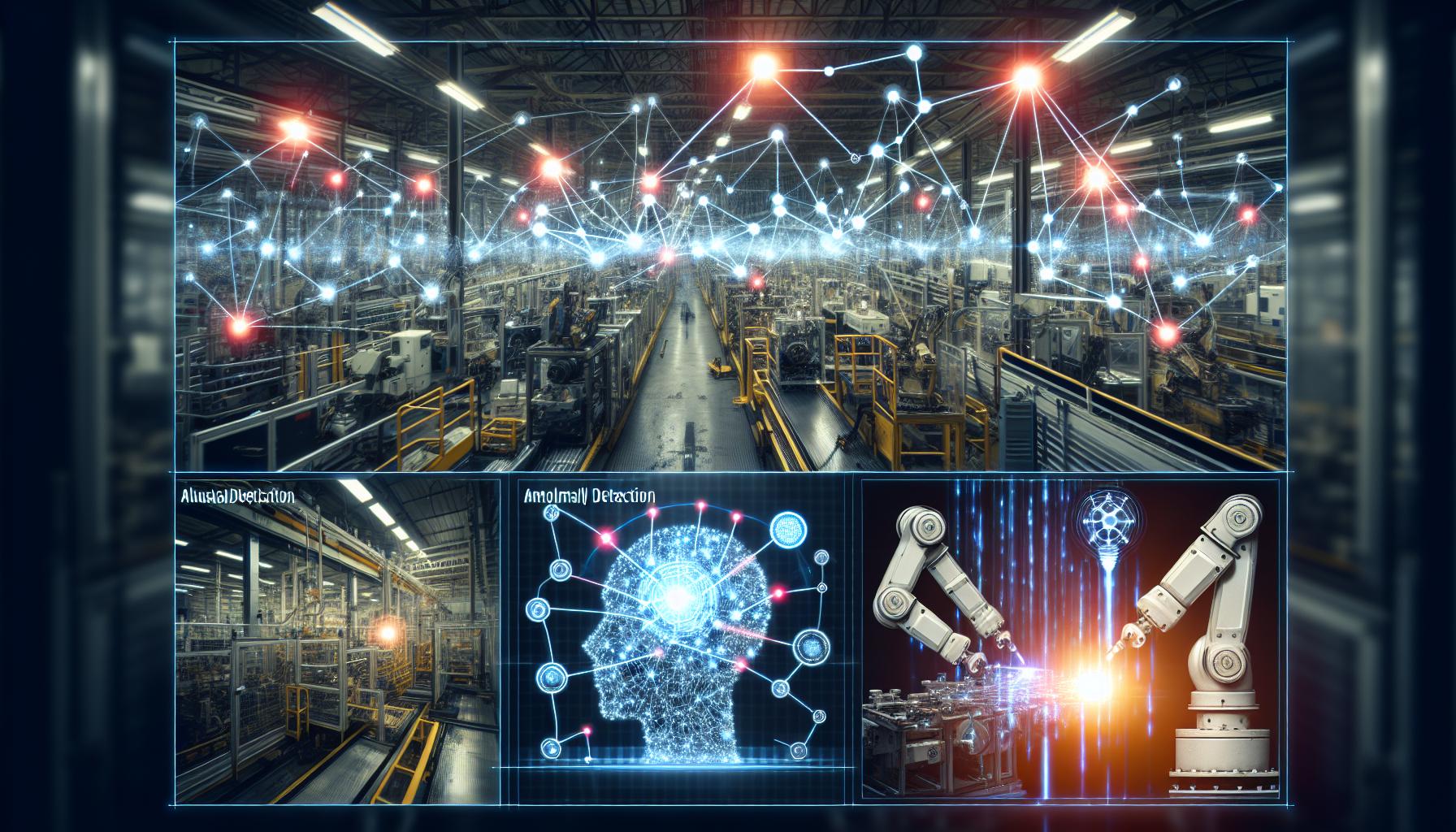
Introduction
In the ever-evolving world of manufacturing, ensuring equipment reliability and minimizing operational downtime are of utmost importance. With the advancements in Artificial Intelligence (AI) and the Internet of Things (IoT), predictive maintenance strategies have taken a dramatic leap. AI agents, embedded within industrial IoT systems, are now outperforming traditional AI interfaces, such as ChatGPT, in the realm of predictive maintenance. This blog explores the significant advantages of using embedded AI agents for continuous equipment monitoring, anomaly detection, and automation of preventive actions. Additionally, we'll delve into case studies from various manufacturing sectors showcasing how embedded AI solutions contribute to reduced maintenance costs and improved equipment uptime.
Continuous Equipment Monitoring
The manufacturing industry relies heavily on the consistent performance of machinery and equipment. Traditional AI interfaces, although intelligent, often require significant human intervention to interpret data and provide actionable insights. In contrast, embedded AI agents in industrial IoT systems constantly monitor equipment in real-time. These agents are designed to process massive amounts of data from numerous sensors installed on machinery. By continuously analyzing this data, AI agents can detect even the slightest deviations from normal operation, which could indicate potential issues.
For example, embedded AI agents can monitor parameters such as temperature, vibration, and pressure to identify patterns that precede equipment failures. Unlike traditional AI interfaces that might require scheduled retrieval and analysis of data, embedded AI agents offer uninterrupted surveillance, resulting in early detection of issues before they escalate. This proactive approach ensures that minor problems are addressed promptly, preventing costly breakdowns and unplanned downtime.
Anomaly Detection
Anomaly detection is a crucial aspect of predictive maintenance, as it enables the identification of abnormal behavior that may indicate impending equipment failure. Embedded AI agents excel in this area by leveraging advanced machine learning algorithms to differentiate between normal and anomalous patterns. These agents can be trained using historical data, enabling them to recognize subtle changes in equipment behavior that may go unnoticed by human operators or traditional AI interfaces.
The continuous monitoring capabilities of embedded AI agents contribute significantly to their effectiveness in anomaly detection. For instance, in a production line, slight changes in the vibration patterns of a conveyor belt motor could indicate a developing issue. Embedded AI agents can detect these anomalies in real-time, triggering alerts for maintenance teams to investigate and address the problem before it leads to a complete failure. This predictive approach not only saves time and resources but also enhances overall equipment reliability and performance.
Preventive Action Automation
Automation of preventive actions is a game-changer in predictive maintenance. Embedded AI agents can go beyond merely identifying potential issues by automating the necessary preventive measures. This capability distinguishes them from traditional AI interfaces that rely on human operators to execute maintenance tasks based on reported findings.
For instance, embedded AI agents can be programmed to automatically adjust operating parameters, initiate diagnostic tests, or schedule maintenance activities without human intervention. This level of automation ensures that preventive actions are taken promptly and consistently, reducing the risk of human error and maximizing the effectiveness of maintenance efforts. Imagine a scenario where an embedded AI agent detects a gradual increase in the temperature of a critical machine component. Without delay, the agent can initiate a cooling process or adjust the machine's operating speed to prevent overheating and potential damage.
Case Studies
Let's delve into some real-world case studies from various manufacturing sectors that demonstrate the efficacy of embedded AI agents in predictive maintenance:
Automotive Manufacturing
In the automotive industry, where precision and reliability are paramount, embedded AI agents have revolutionized predictive maintenance. A leading automobile manufacturer integrated AI agents into their production line's IoT network to monitor robotic arms responsible for assembling car components. The agents continuously analyzed data, predicting wear and tear on the joints and motors of the robotic arms. By detecting anomalies early, the manufacturer was able to schedule maintenance during planned downtime, minimizing production disruptions and reducing maintenance costs by 30%.
Food and Beverage Production
The food and beverage sector also benefits from embedded AI agents for predictive maintenance. A large beverage company implemented AI-enabled IoT systems to monitor critical equipment such as bottling machines and refrigeration units. The embedded AI agents detected minor fluctuations in operational parameters, indicating potential issues with the machines' components. By automatically scheduling maintenance activities and adjusting operating conditions, the company witnessed a 25% increase in equipment uptime and a significant reduction in product spoilage due to equipment failures.
Energy Sector
The energy sector relies heavily on the continuous operation of equipment like turbines and transformers. An energy company deployed embedded AI agents within their IoT infrastructure to monitor the performance of wind turbines. The AI agents analyzed vibration data and identified early signs of blade fatigue and misalignment. By initiating timely maintenance activities, the company reduced downtime by 40% and extended the lifespan of their turbines, resulting in substantial cost savings.
Conclusion
The integration of embedded AI agents within industrial IoT systems marks a transformative shift in predictive maintenance strategies across various manufacturing sectors. These agents offer continuous equipment monitoring, advanced anomaly detection, and automation of preventive actions, setting them apart from traditional AI interfaces like ChatGPT. Real-world case studies from the automotive, food and beverage, and energy sectors exemplify the tangible benefits of embedded AI solutions, including reduced maintenance costs and improved equipment uptime. As manufacturing continues to evolve, embedded AI agents will play an increasingly pivotal role in achieving operational excellence and maintaining competitive advantage.